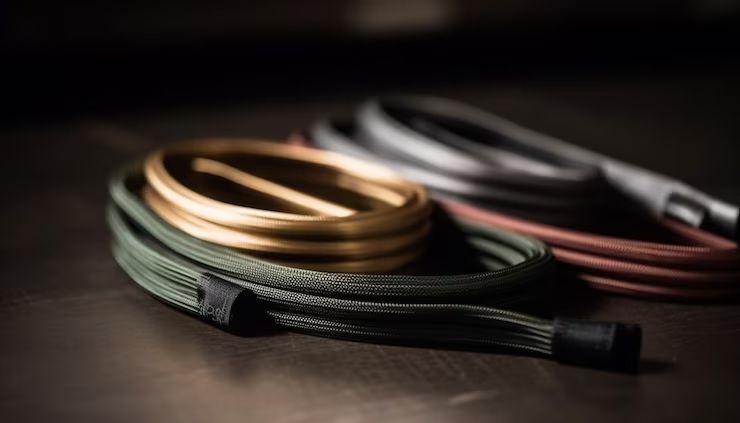
Cables are the hidden workhorses of our connected society. They deliver power to our homes and industries, carry the data for our communications, and enable critical control systems. We often take them for granted until they fail, causing potentially disruptive outages, costly downtime, and safety concerns. While manufacturers ensure cables meet stringent quality standards upon production, the real world presents ongoing challenges – installation stresses, environmental exposure, operational wear, and tear. What if we could monitor the health of these vital assets after they're installed, getting early warnings of potential trouble? This is precisely what the Internet of Things (IoT) makes possible, deploying smart sensors to provide continuous, real-time insights into cable condition, significantly boosting reliability.
Why Monitor Cables Beyond the Factory?
A cable's life truly begins once it's put into service. Out in the field – whether buried underground supporting Mumbai's growing infrastructure, routed through a harsh industrial environment, or strung across transmission towers – cables face a barrage of stresses that can degrade them over time:
- Installation Effects: The physical act of pulling, bending, terminating, and joining cables can introduce stresses or minor imperfections.
- Environmental Factors: Exposure to fluctuating temperatures, moisture, corrosive soils or chemicals, UV radiation from sunlight, or even physical impacts can accelerate aging.
- Operational Stresses: Constant or fluctuating electrical loads generate heat, nearby machinery can cause vibrations, and ground movement can strain buried cables.
These factors can lead to gradual deterioration – insulation breakdown, connection degradation, conductor fatigue – eventually culminating in failure. IoT sensors offer a way to detect the subtle signs of this degradation long before it becomes critical.
How IoT Sensor Monitoring Works
Think of it as giving cables a continuous, remote health check-up:
- The Sensors: Compact, often ruggedized sensors are strategically attached to the cable or placed in its immediate vicinity. These are designed to measure specific parameters indicative of cable health.
- Data Capture: The sensors take periodic or continuous measurements of parameters like temperature, vibration, strain, or electrical characteristics.
- Wireless Transmission: This data is sent wirelessly over networks designed for low power and potentially long range (like LoRaWAN, NB-IoT, Sigfox, or sometimes cellular/5G for higher bandwidth needs) to a central data platform, often hosted in the cloud.
- Data Analysis & Interpretation: Software platforms receive the data streams and apply analytical algorithms. This can range from simple threshold alerts (e.g., temperature exceeding a limit) to complex pattern recognition using AI and machine learning to identify subtle anomalies or predict future degradation trends.
- Alerts & Action: When the analysis flags a potential issue or a concerning trend, automated alerts are dispatched to maintenance teams, providing specific information about the location and nature of the potential problem, enabling targeted investigation and proactive intervention.
What Are These Sensors Measuring? Key Parameters
The specific sensors deployed depend on the type of cable and the potential failure modes being monitored:
- Temperature: A fundamental indicator, especially for power cables. Elevated temperatures can signal high-resistance connections (a common failure point), overloading conditions, or insulation degradation. Distributed Temperature Sensing (DTS) using fiber optics integrated into or alongside the cable can even provide a temperature profile along its entire length.
- Vibration & Acoustics: Sensors can detect abnormal vibrations caused by loose mountings or nearby equipment, which can fatigue components. Acoustic sensors might pick up the specific sound signatures associated with partial discharge activity within insulation.
- Strain / Mechanical Stress: Strain gauges can monitor physical tension, compression, or bending, particularly important for cables in dynamic applications (robotics), aerial cables subject to wind/ice loading, or buried cables in areas prone to ground movement.
- Partial Discharge (PD): Highly relevant for medium and high-voltage cables. Specialized sensors (acoustic, ultrasonic, RF, or HFCTs) detect the small electrical discharges that occur within insulation voids or defects. These are often precursors to catastrophic insulation failure, making early detection vital.
- Environmental Conditions: Sensors measuring ambient temperature, humidity, water presence (for underground vaults), or specific corrosive agents provide context about external factors influencing cable health and aging.
The Value Proposition: Benefits of IoT Monitoring
Deploying IoT sensors for cable monitoring delivers compelling advantages:
- Shift to Predictive Maintenance: This is the core benefit. Instead of reacting to failures or performing potentially unnecessary time-based inspections, maintenance becomes proactive, driven by data indicating the actual condition of the cable and predicting potential issues before they occur.
- Reduced Unplanned Downtime: By catching problems early, repairs can be scheduled during planned maintenance windows, drastically reducing costly emergency outages and associated production/service losses.
- Enhanced Safety: Early detection of conditions like severe overheating, insulation breakdown (via PD), or critical mechanical strain can prevent potential fires, electrical faults, or structural failures.
- Optimized Asset Lifespan: Addressing issues like connection hotspots or excessive stress promptly can slow down degradation, potentially extending the reliable service life of expensive cable assets.
- Efficient Maintenance Resource Allocation: Maintenance teams focus their efforts where data indicates a need, rather than spending time on routine inspections of healthy assets.
- Improved Network Reliability & Stability: For utilities and critical infrastructure operators, preventing cable failures leads directly to more dependable service delivery.
Applications Across Industries
IoT-based cable monitoring finds value in numerous sectors:
- Power Transmission & Distribution: Monitoring underground networks, substation cabling, and overhead lines for utilities.
- Industrial Plants: Keeping track of critical power and control cables for machinery in manufacturing, processing, chemical plants, especially in harsh environments.
- Renewable Energy: Monitoring the extensive cabling networks in solar farms and wind farms to ensure efficient power generation.
- Telecommunications: Detecting physical damage or stress on fiber optic or coaxial cables vital for communication networks.
- Transportation: Monitoring cables in railway signaling systems, tunnels, bridges, and airports where reliability is critical.
Implementation Challenges
Adopting this technology involves considerations:
- Sensor & Installation Costs: The initial investment in sensors, network gateways, data platforms, and the labor to install sensors (especially retrofitting existing infrastructure) needs careful evaluation.
- Sensor Powering Strategy: Ensuring long-term power for sensors in diverse locations (remote, underground) via long-life batteries or reliable energy harvesting is crucial.
- Connectivity Reliability: Achieving consistent wireless data transmission from potentially challenging environments (underground, inside metal enclosures, remote areas) requires careful network planning.
- Data Management & Analytics: Effectively processing, storing, and analyzing the potentially large volumes of sensor data to extract actionable insights requires appropriate software platforms and potentially data science expertise.
- Cybersecurity: Protecting the IoT devices, communication network, and data platform from cyber threats is non-negotiable.
Foundation of Quality
It's worth remembering that monitoring enhances, but doesn't replace, the need for quality components. Starting with robust, well-manufactured cables from reputable sources like established cable manufacturers in uae, potentially using materials from certified quality cable suppliers in uae, provides the best foundation. IoT monitoring then adds a layer of ongoing vigilance throughout the cable's operational life.
Conclusion: Giving Cables a Voice for Reliability
Utilizing IoT sensors represents a significant evolution in how we manage and maintain critical cable infrastructure. By providing a continuous, data-rich view of cable health directly from the field, this technology enables a powerful shift from reactive repairs to proactive, condition-based maintenance. This data-driven approach not only enhances the safety and reliability of essential systems but also optimizes maintenance expenditure and potentially extends the functional life of these vital assets. IoT is effectively giving our cables a voice, allowing us to listen for signs of trouble and act intelligently before silence falls.
Your IoT Cable Monitoring Questions Answered (FAQs)
- How exactly are IoT sensors attached to existing cables without damaging them?
Various non-intrusive methods are used. Sensors might be clamped around the cable's outer jacket, attached using specialized industrial adhesives, integrated into splice boxes or termination points, or placed in close proximity (e.g., magnetic sensors for current, acoustic sensors nearby for PD). The specific method depends on the sensor type and application. - How long do the batteries in these wireless sensors typically last?
Sensor and battery technology has advanced significantly. Many IoT sensors designed for infrastructure monitoring utilize ultra-low-power communication protocols and optimized electronics, allowing batteries to last anywhere from 3 to 10+ years, depending on the sensor type, measurement frequency, and environmental conditions. - Is the data from these sensors secure?
Security is a critical design consideration for reputable IoT systems. Measures typically include data encryption during transmission and storage, secure device authentication (ensuring only authorized sensors can connect), secure network protocols, and access controls on the data platform. However, implementing robust cybersecurity practices is essential. - What is "Partial Discharge (PD)" and why is it important to detect?
Partial Discharge refers to small electrical sparks or discharges that occur within voids, defects, or contaminants in the insulation of medium and high-voltage cables. While small initially, PD activity gradually degrades the insulation over time and is a common precursor to eventual insulation breakdown and cable failure. Detecting PD early allows for intervention before a major fault occurs. - Can IoT monitoring predict exactly when a cable will fail?
It's more about predicting probability and detecting anomalies than predicting an exact failure date. By tracking trends (e.g., rising temperature, increasing PD activity, growing strain), the system can indicate that a cable is degrading and its risk of failure is increasing significantly, allowing maintenance teams to prioritize action. It provides early warnings, not a crystal ball.